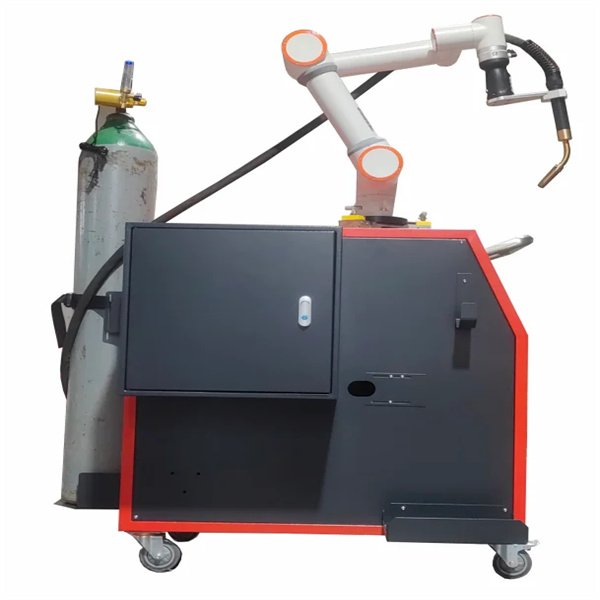
The Importance of Automated Welding Robots in Industrial Production
In today’s fast-paced industrial landscape, efficiency and precision are key to staying competitive. One of the most transformative innovations in manufacturing has been the rise of the automated welding robot. These advanced machines have revolutionized the way industries approach welding, offering a range of benefits including increased productivity, improved weld quality, and significant cost savings. Whether in automotive manufacturing, aerospace, or heavy industries, the automated welding robot is now an indispensable tool.
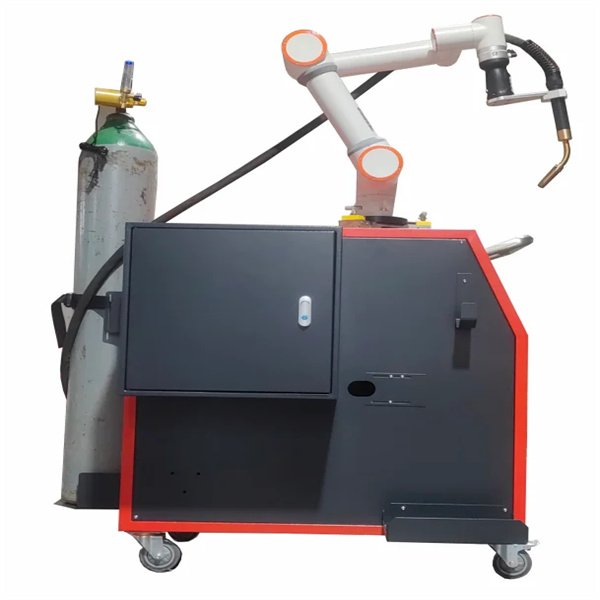
1. The Rise of Automated Welding Robots
The use of robots in welding isn’t a new concept, but the development of the automated welding robot has taken industrial production to new heights. Traditionally, welding was a manual process that required skilled labor, which often resulted in inconsistencies and longer production times. Automated welding robots, on the other hand, work with extreme precision, repeatability, and speed. These robots can handle complex and repetitive tasks, ensuring high-quality results every time, reducing the likelihood of human error.
Modern automated welding robots use advanced sensors, cameras, and AI-driven systems to adapt to varying conditions on the production floor. They can handle tasks such as MIG, TIG, and laser welding, making them incredibly versatile and adaptable to different types of welding jobs. The robots can be programmed to complete welds at optimal speeds and with minimal supervision, making them a vital part of high-output industries.
2. Benefits of Automated Welding Robots in Production
2.1 Enhanced Productivity
One of the primary advantages of using an automated welding robot is the significant increase in production efficiency. Unlike manual welding, which is dependent on human operators, robots can work continuously without the need for breaks or rest. This results in a dramatic boost in throughput, allowing companies to meet production targets faster and more efficiently.
Automated welding robots can also work in challenging environments that would otherwise be unsafe for human workers. For example, in high-temperature areas, robots can perform welding tasks without risking the health and safety of workers. This opens up new possibilities for industries such as shipbuilding, nuclear power, and heavy machinery manufacturing.
2.2 Consistent and High-Quality Results
Another compelling reason to integrate an automated welding robot into industrial production is the consistency and precision it offers. Humans can introduce variability into welding processes due to factors such as fatigue, skill level, or environmental distractions. However, robots are programmed to follow exact specifications and can execute each weld with the same level of precision, regardless of the time of day or the complexity of the task.
This consistency is crucial in industries where high-quality welds are non-negotiable, such as in aerospace and automotive production, where even the smallest deviation can lead to costly defects or failures. The automated welding robot ensures that every weld meets the stringent quality standards set by industry regulations.
2.3 Cost-Effectiveness
Though the initial investment in automated welding robots can be significant, the long-term savings far outweigh the upfront costs. With robots taking over the more repetitive and labor-intensive welding tasks, companies can reduce the number of manual workers needed for welding operations. This not only cuts down on labor costs but also reduces the risk of workplace injuries associated with manual welding, leading to lower insurance premiums and fewer worker compensation claims.
Moreover, automated systems can improve the use of raw materials. By applying precise welding techniques, robots minimize waste and increase the overall yield of materials, providing a more sustainable approach to production.
2.4 Flexibility and Scalability
One of the key advantages of automated welding robots is their flexibility. Unlike manual labor, which is limited by human capabilities, robots can be quickly reprogrammed to perform different welding tasks, making them ideal for companies that need to adjust their production lines quickly. This adaptability allows manufacturers to keep pace with changing market demands without having to invest in new infrastructure.
For example, industries with frequent product redesigns or those involved in small-batch production can benefit from the flexibility of automated welding robots. Robots handle a variety of materials, from steel and aluminum to composites, and equip themselves with different welding tools based on the requirements of each project.
3. The Role of FAIRINO Welding Automation Robots
As the demand for automated welding technology continues to grow, companies are looking for reliable automated welding robot solutions. One such solution comes from FAIRINO welding automation robots. FAIRINO is a leading manufacturer known for providing cutting-edge welding automation systems that cater to a wide range of industries. Their robots are designed with a focus on precision, flexibility, and ease of use, making them an ideal choice for manufacturers seeking to integrate automation into their production processes.
The FAIRINO welding automation robots feature advanced capabilities, such as precise motion control, high-load capacity, and adaptive welding, allowing them to handle the most demanding welding applications. The robots’ intuitive programming interfaces make them accessible to companies of all sizes, whether they are new to automation or looking to upgrade their existing systems.
With their robust design and cost-effective pricing, FAIRINO welding automation robots are ideal for companies looking to scale up their production while maintaining high standards of quality. The robots are also backed by strong customer support, providing manufacturers with the guidance they need to optimize their operations.
4. The Future of Welding Automation
The future of welding automation looks incredibly promising, with advancements in robotics, artificial intelligence, and machine learning driving further innovations in automated welding. As technology continues to evolve, automated welding robots will become even more intelligent, adapting in real-time to the varying conditions in the production environment.
The integration of AI into automated welding robots will allow for even greater precision and optimization. These systems will be able to learn from each weld, automatically adjusting parameters to ensure the best possible result. In addition, as industrial Internet of Things (IIoT) networks become more widespread, automated welding robots will be able to communicate with other machines on the production line, creating a fully integrated, smart factory environment.
The need for skilled labor in welding will also change. While robots will take on many of the physically demanding tasks, there will still be a need for workers to oversee, maintain, and optimize these systems. This shift will require a new generation of workers with expertise in robotics, programming, and system integration.
5. Conclusion
The automated welding robot is no longer just a trend—it is a critical component of modern industrial production. With benefits such as enhanced productivity, consistency, cost-effectiveness, and scalability, these robots are reshaping the manufacturing landscape. Companies that adopt automation can achieve higher levels of precision, improve worker safety, and increase their overall competitiveness in the market.
For businesses looking to invest in cutting-edge welding automation, FAIRINO welding automation robots offer an excellent solution. As a trusted automated robotic welding provider, FAIRINO offers advanced capabilities and user-friendly design, making their robots a smart investment for the future of industrial production. With their versatile features, these robots are built to meet the diverse needs of industries, ensuring high-quality results with minimal downtime.