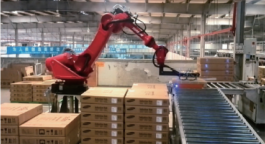
Managing the Deployment Strategy of Automation Robots
Industrial automation has brought revolutionary material handling technologies, and Automation-Ready Collaborative Robots have pioneered this. Robots differ from conventional industrial robots in that they can collaborate in workplaces with human employees without harming them. Therefore, they are especially adept at working with Handling Robot Workstations in manufacturing, warehousing, and logistics. This paper offers the best practice on the deployment of Handling Automation Robots such that integration is efficient, seamless, and safe to execute on factory floors.
1. Orienting Automation-Ready Robots
New robots are shipped with some inherent safety features such as force-limiters, collision detection, and programmable interfaces that are simple to use. These render them automation-ready, and they can be installed right away without protection cages.
Key Advantages of Robots Performing Work:
- Flexibility: Easy to reprogram for new applications (e.g., pick-and-place, palletizing).
- Safety: Can work in contact with people without cages (where suitably risk-assessed).
- Ease of Integration: Coupled with current Handling Robot Workstations via plug-and-play interfaces.
- Cost-Effectiveness: Lower initial capital expense than traditional industrial robots.
2. Ideal Handling Robot Workstation Design
Maximum productivity and safety are achieved by the implementation of an optimal Handling Robot Workstation configuration. The most compelling reasons to implement are the following:
A. Workstation Optimization
- Human Ergonomic Design: Human ergonomic design to facilitate safe human-robot interaction.
- Modular Installation: Modular installation to permit remounting in order to handle different types of payloads.
- Safety Zones: Utilization of light curtains or laser scanners for added protection.
B. End-Effector Selection
- Grippers: Vacuum, pneumatic, or electrical grippers based on payload and material.
- Tool Changers: Can be used for easy tool changing of end-effectors to facilitate easy changeovers of tasks.
C. Sensor and Conveyor Integration
- Automated Guided Vehicles (AGVs): AGVs are unloaded/loaded by robots to prevent material flow disruption.
- Vision Systems: The sensors and cameras allow proper object detection as well as processing objects.
3. Step-by-Step Handling Automation Robot Installation
Step 1: Feasibility Study & Task Analysis
- Select the highest potential repeat handling tasks for automation.
- Quote payload, reach, and cycle time specifications.
Step 2: Robot & Payload Selection
- Pick robots with a particular payload capacity (e.g., UR10e for 12.5 kg, FANUC CRX for 20 kg).
- Suffix compatible with installed automation hardware.
Step 3: Risk & Safety Assessment
- Conduct risk assessment in compliance with ISO/TS 15066 (collaborative robot safety standard).
- Safety-rated guarded stops or co-working area guarded stops for speed reduction.
Step 4: Programming & Simulation
- No-code or drag-and-drop script (i.e., Polyscope of Universal Robots, Teach Pendant of FANUC).
- Robot runtime within programming software such as Robot Studio or Visual Components should be automated before installation.
Step 5: Installation & Calibration
- Install the robot on a mobile base or work cell in a safe location.
- Force-torque sensors and vision systems are to be calibrated for use to the maximum.
Step 6: Operator Training & Continuous Improvement
- Robot emergency procedures and robot operators are to be trained.
- The most efficient workflow with performance tracking is to be provided for use to the maximum.
4. Material Handling Robot Applications
Applications of robots are transforming material handling in manufacturing plants:
A. Assembly & Manufacturing Lines
- Loading and unloading of CNC machinery.
- Kitting and sorting.
B. Warehousing & Logistics
- Palletizing and depalletizing.
- Automated label and packaging.
C. Pharmaceutical & Food Industries
- Clean handling of products without contamination.
- Compliance with hygienic design.
5. Automation Management Future Trends
- Machine Learning Robots: Robotic using machine learning to perform adaptive grasping and path optimization.
- Mobile Manipulation: AMR-enabled robotics.
- Cloud-Based Robot Management: Remote monitoring as well as predictive maintenance.
6. Conclusion
Installation of Automation-Ready Collaborative Robots onto Robot Workstations for Handling involves time-consuming planning from task analysis up to adherence to required safety standards. Using the Handling Automation Robots, manufacturers have increased productivity, minimized labor expense, and ensured a better workplace. With every new technology, robots will remain smart, advanced, and high-technology industrial automation in history books.
Through implementing best practices in robot deployment, organizations can maximize the potential of collaborative robots utilized for material handling.