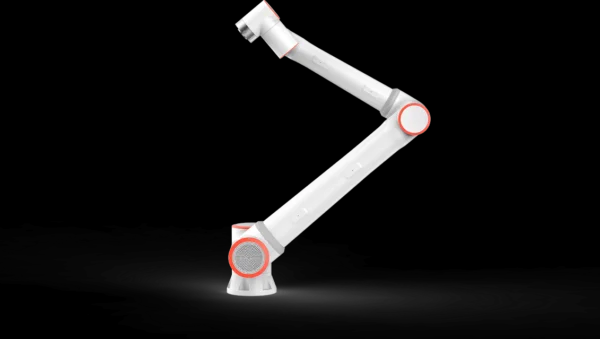
Analysis of the Core Components of Assembly Automation Robots
Assembly automation robots have revolutionized the manufacturing industry by increasing productivity, precision, and flexibility. These robots automate the assembly processes, reducing the need for humans to intervene in tasks that can be repetitive, dangerous, or require high accuracy. Whether used in automotive production, electronics, or consumer goods manufacturing, assembly automation robots play a key role in streamlining operations. In this blog, we will analyze the core components that make up assembly automation robots, shedding light on how they function and why they are essential to modern production lines.
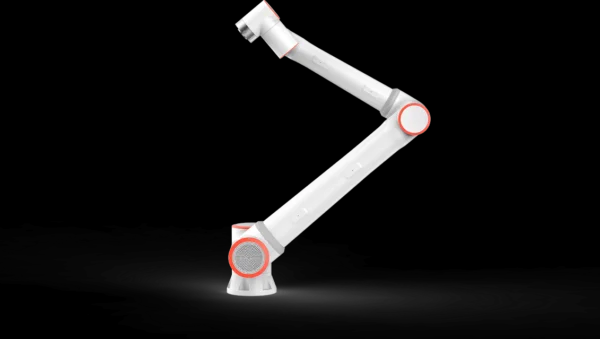
1. Robot Arm: The Heart of the Assembly Process
The assembly robot arms are arguably the most crucial component of an assembly automation robot. These robotic arms are responsible for performing the physical tasks, such as picking, placing, screwing, and welding components. These arms are highly versatile and can be customized for a variety of tasks depending on the application.
Key Features of Assembly Robot Arms:
Degrees of Freedom (DOF): The number of degrees of freedom in an assembly robot arm determines its flexibility and precision.. More DOF allows the robot to perform more complex and varied tasks. Most industrial robotic arms have at least six DOF, enabling them to move in multiple directions and orientations.
End Effectors: The end effector of a robot arm is the tool or device that interacts with the assembly objects. Common end effectors include grippers, suction cups, or specialized tools for tasks like screwing or welding. The design and functionality of the end effector are tailored to specific assembly needs.
Actuators: The actuators in the robot arm control the movement of each joint. These can be electric, pneumatic, or hydraulic, and they provide the necessary force and precision to perform delicate or heavy-duty tasks. Electric actuators are commonly used in assembly automation robots due to their precision and ease of control.
Importance of Robot Arms in Assembly:
The assembly robot arms are designed to work with high precision, ensuring that the assembly process is consistent and error-free. They can handle multiple tasks simultaneously, reducing the time required for each part of the production cycle. Whether it’s fastening screws, placing components in place, or picking up objects, the robot arms are at the forefront of modern assembly operations.
2. Control System: The Brain of the Robot
The control system of an assembly automation robot is the software and hardware that manage the robot’s actions. This system receives input from sensors, processes the data, and sends commands to the robot’s actuators to perform the desired actions.
Key Features of the Control System:
Robot Programming: Operators can program modern assembly automation robots using various methods, including manual teaching, offline programming, or programming through a computer-aided design (CAD) system. The programming allows the robot to perform specific tasks such as sequencing, part placement, and quality inspection.
PLC and HMI Integration: Many assembly robots are integrated with programmable logic controllers (PLC) and human-machine interfaces (HMI). The PLC manages the overall workflow, while the HMI allows operators to monitor and control the robot. This integration ensures smooth communication between robots and other machinery on the production line.
Safety Protocols: Advanced control systems also include safety features, such as collision detection and emergency stop functions. These systems ensure the robot operates safely around human workers, especially in environments where collaborative robots (cobots) are used.
Why Control Systems Matter:
The control system is essential for ensuring that the robot performs tasks with high precision and efficiency. By accurately processing input from sensors and environmental data, the control system enables robots to make real-time adjustments to their actions, thereby improving the overall quality of the assembly process.
3. Sensors: Enhancing Precision and Autonomy
Sensors are critical components in assembly automation robots, as they allow the robot to perceive its environment and make decisions based on that information. These sensors help the robot perform tasks with high precision and enable it to work autonomously in complex environments.
Types of Sensors in Assembly Robots:
Vision Systems: Cameras and vision sensors allow robots to “see” their environment. By analyzing images, the robot can detect the position of components, verify alignment, or check for defects in the parts being assembled.
Force Sensors: These sensors measure the force applied by the robot arm when handling objects. Force sensors are essential when performing delicate operations such as screwing or inserting components, where applying too much or too little force could cause errors or damage.
Proximity Sensors: Proximity sensors help the robot detect the presence of objects nearby. These sensors are essential for tasks like pick-and-place, as they ensure the robot’s arms interact with components only when they are in the correct position.
The Role of Sensors in Efficiency:
Sensors enhance the flexibility and autonomy of assembly automation robots. By giving robots the ability to perceive their surroundings and adjust their actions accordingly, sensors improve the accuracy of tasks and reduce the likelihood of mistakes. This ability to work in dynamic environments also allows robots to adapt to different parts and assembly lines, enhancing overall production flexibility.
4. Power Supply: Ensuring Reliable Operation
The power supply is the backbone of any assembly automation robot. It ensures that the robot’s actuators, sensors, and control systems receive the necessary energy to operate effectively. Power supply units can vary depending on the robot’s requirements, with most robots relying on electrical power, though some may use compressed air or hydraulic systems for specific tasks.
Importance of a Reliable Power Supply:
The reliability of the power supply directly impacts the efficiency and uptime of the robot. Inconsistent or insufficient power can cause the robot to malfunction, leading to delays in production or even equipment failure. Choosing a reliable power source and ensuring that it is properly maintained is key to the long-term performance of assembly automation robots.
Conclusion
The core components of assembly automation robots include robot arms, control systems, sensors, power supplies, and integration capabilities. These components work together to create a highly efficient and reliable system. This system automates assembly tasks effectively. By leveraging the capabilities of these components, manufacturers can achieve significant improvements in productivity, precision, and cost-effectiveness.
For those looking to implement or upgrade their assembly lines, working with a trusted assembly automation robots manufacturer can provide valuable insights and access to cutting-edge technology. Whether you’re looking to improve your production processes, enhance quality control, or reduce operational costs, assembly automation robots offer a versatile and scalable solution to meet your needs.