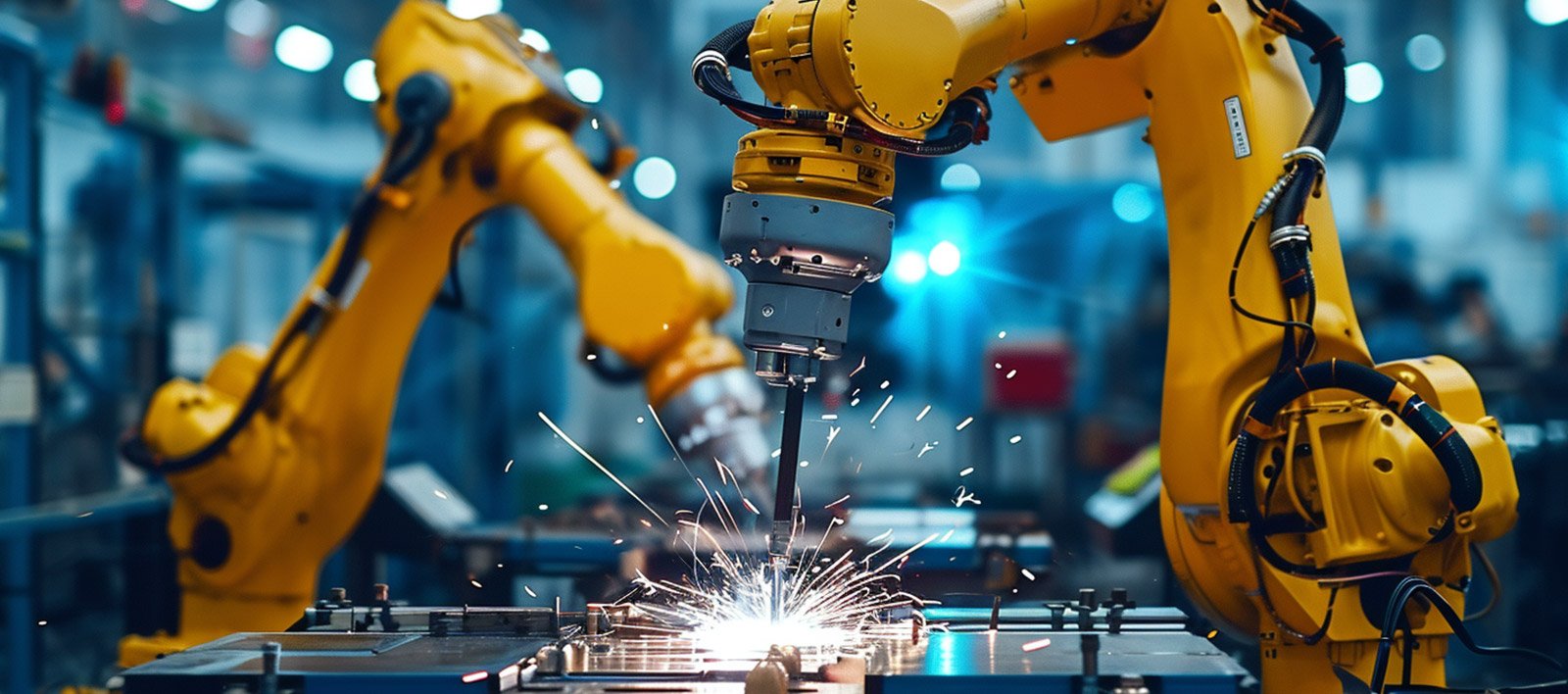
How to Ensure the Safety of Collaborative Palletizing Robots in Your Facility
In today’s automated manufacturing world, collaborative palletizing robots have become a vital tool in improving efficiency and reducing labor costs. These robots are designed to work alongside human operators, making them an ideal solution for tasks like product stacking, sorting, and packaging. However, as with any advanced technology, ensuring the safety of these machines is critical to prevent accidents and maximize productivity.
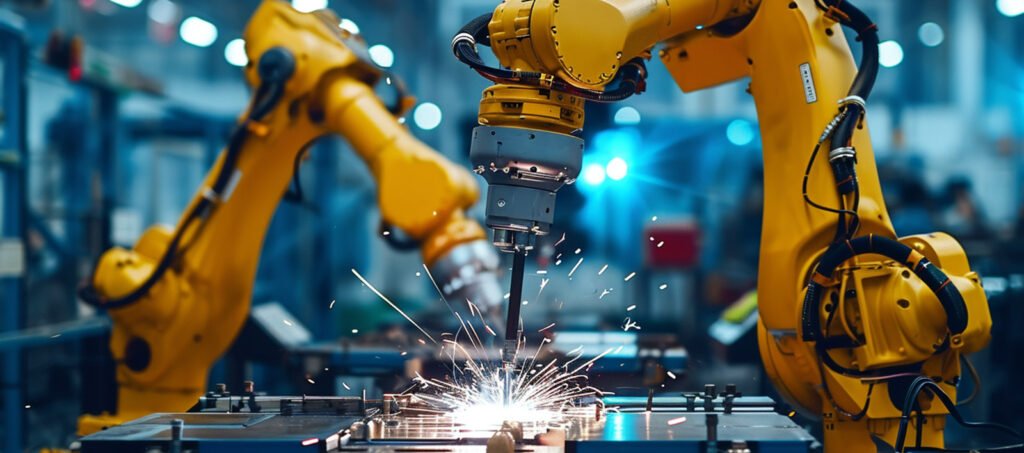
Understanding Collaborative Palletizing Robots
Collaborative palletizing robots are designed to work in close proximity to humans, performing tasks like pallet stacking, product sorting, and packaging with minimal human intervention. Unlike traditional industrial robots, these robots are equipped with advanced sensors and safety features that allow them to interact safely with their human counterparts. They are widely used in industries like logistics, food and beverage, pharmaceuticals, and consumer goods, where high throughput and efficiency are required.
However, while these robots bring significant operational benefits, their integration into the workplace must be handled with care to ensure the safety of employees. Ensuring proper safety protocols is essential to avoid accidents, injuries, and machine malfunctions.
Key Safety Strategies for Collaborative Palletizing Robots
1. Investing in Safety Features and Sensors
One of the primary safety measures for collaborative palletizing robots is equipping them with safety sensors. These sensors are responsible for detecting objects and humans in the robot’s vicinity. For example, advanced proximity sensors and vision systems enable the robot to stop or slow down its movement if it senses an obstruction. Force and torque sensors are also critical as they allow the robot to detect unexpected contact, such as a collision with a human operator, and automatically stop the robot’s motion to prevent injury.
In addition to these safety features, collision detection systems are essential to ensure that the robot doesn’t unintentionally come into contact with other equipment or workers. A collaborative palletizer manufacturer will typically incorporate these safety features into the design of the robot, ensuring that the system meets the necessary industry standards for safety.
2. Implementing Safe Human-Robot Interaction Protocols
A key feature of collaborative palletizing robots is their ability to work alongside human operators in shared spaces. However, to minimize risks, it’s crucial to establish safe interaction protocols between humans and robots. One of the most effective ways to ensure safe human-robot collaboration is through the use of “safety zones” or designated workspaces. These zones help ensure that humans and robots don’t occupy the same space at the same time, reducing the likelihood of accidental collisions.
In cases where humans and robots must share a space, it is important to integrate communication systems that allow the robot to inform the operator of its movements. Some robots are equipped with warning lights or sound signals to alert nearby workers of impending movements. Training employees on how to safely interact with collaborative robots and establishing clear communication methods are also vital components of a safe workplace.
3. Regular Maintenance and Calibration
Routine maintenance and calibration are key to ensuring the long-term safety and performance of collaborative palletizing robots. Regularly checking the robot’s mechanical components, sensors, and safety systems can help identify potential issues before they lead to accidents. Wear and tear on joints, actuators, and other moving parts can cause malfunctioning or unpredictable movements, posing a safety risk to workers.
Calibration of the robot’s sensors and safety features is also necessary to ensure their accuracy and functionality. A collaborative palletizer manufacturer will provide guidelines for regular maintenance and calibration, including the necessary tools and procedures for keeping the robot in peak working condition.
4. Establishing Emergency Stop Mechanisms
In any automated environment, having a reliable emergency stop mechanism is crucial for ensuring safety. In the case of a malfunction, power surge, or a safety hazard, an emergency stop function allows operators to immediately halt the robot’s movements, minimizing the risk of injury. These stop mechanisms should be easily accessible and visible to all employees working near the robot.
It is important that operators are well-trained on how to activate the emergency stop and understand when it should be used. Additionally, collaborative palletizing robots should be equipped with automatic shutdown features if an anomaly is detected in the robot’s performance or sensors.
5. Monitoring and Data Logging for Continuous Improvement
Another effective way to ensure safety is through continuous monitoring and data logging. Modern collaborative palletizing robots often come equipped with monitoring systems that allow operators to track the robot’s performance, detect anomalies, and monitor the safety features in real-time. This data can provide valuable insights into how the robot is performing and whether any safety adjustments are required.
By regularly reviewing the data logs, manufacturers can also identify patterns that may indicate potential safety concerns, allowing them to make adjustments before a problem arises. These data logs can also be used to evaluate the efficiency of safety protocols, such as collision detection or emergency stop systems.
Conclusion
Ensuring the safety of collaborative palletizing robots in your facility is essential for maintaining a productive and injury-free working environment. By investing in the right safety features, establishing clear interaction protocols, and regularly maintaining the robot, you can minimize the risk of accidents and maximize the benefits of automation. Whether you are looking for a collaborative palletizer for sale or seeking advice from a reputable collaborative palletizer manufacturer, ensuring the safety of these systems should always be a top priority. With the right safety measures in place, collaborative robots can significantly enhance your business operations while ensuring the well-being of your workforce.